DBTによる表面改善
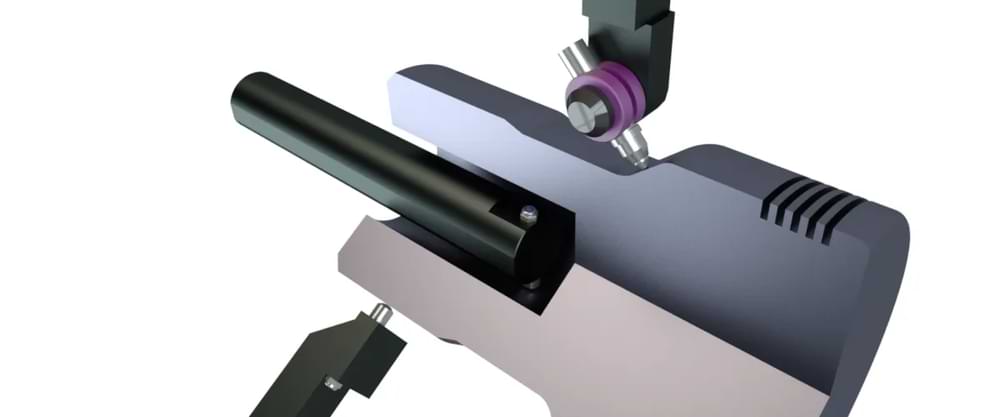
現在、硬化鋼は自動車分野で広く応用されており、ピニオン、カムシャフト、クランクシャフト、クラウンホイールの製造に使用されています。これらの部品は通常、動的負荷条件下で動作するため、その疲労強度は高いレベルであるべきです。
これらの部品の硬度が45 HRCを超えると、その加工は硬いと説明されます。
精密硬旋削は、硬化部品の加工において従来の研削を置き換える能力があるため、産業分野での使用が劇的に拡大しました。
しかし、後に硬旋削では十分な表面仕上げや適切な硬度が得られず、引張残留応力が発生し、疲労寿命に悪影響を及ぼすことが判明しました。
したがって、硬旋削の限界を克服するためには、適切な表面の完全性を得るために、スライドダイヤモンドバーニッシングのような仕上げ操作が必要です。
ダイヤモンドバーニッシングは、切りくず除去を伴わない旋削に似た仕上げプロセスであり、球状に研磨されたダイヤモンドを持つ変形ツールが、ワークピースの表面を圧力下で滑ることで塑性変形を引き起こします。
このプロセスの主な利点は、耐食性と耐摩耗性の向上、微小硬度の増加、表面粗さの低減、圧縮残留応力の誘発、表面の微細構造の改善です。
その結果、ワークピースの疲労強度が向上します。これらの利点により、硬旋削された鋼部品の研削をダイヤモンドバーニッシングで置き換えることが可能になります。
従来の旋盤とCNC旋盤の両方が、バーニッシングプロセスの実行に主に使用されます。ワークピースが回転する際に、バーニッシングヘッドがそれに対して押し付けられ、軸方向に移動します。ダイヤモンドバーニッシングプロセスの基本的な制御パラメータは、
バーニッシング力(, N)、
バーニッシング送り(, mm/rev)、
部品の回転速度(, rpm)、
またはバーニッシング速度(, m/min)、
およびダイヤモンド半径の摩耗(, mm)です。
これまでに、多くの研究が、表面粗さ、表面残留応力、微小硬度、微細構造など、ダイヤモンドバーニッシングプロセスの出力に対するバーニッシングパラメータとその相互作用の影響を調査するために行われてきました。
これらの研究の結果は、ダイヤモンドバーニッシングプロセスの効果が、適用されるバーニッシングパラメータの範囲とその相互作用、バーニッシュされた材料の種類とその硬度、バーニッシングプロセスの環境(潤滑やダイヤモンド半径の摩耗など)に大きく依存することを示しています。
ダイヤモンドバーニッシングプロセスが結果として生じる表面粗さに与える影響を調査するために、以下のリンクを提供します。