ダイヤモンド・バニシングツール
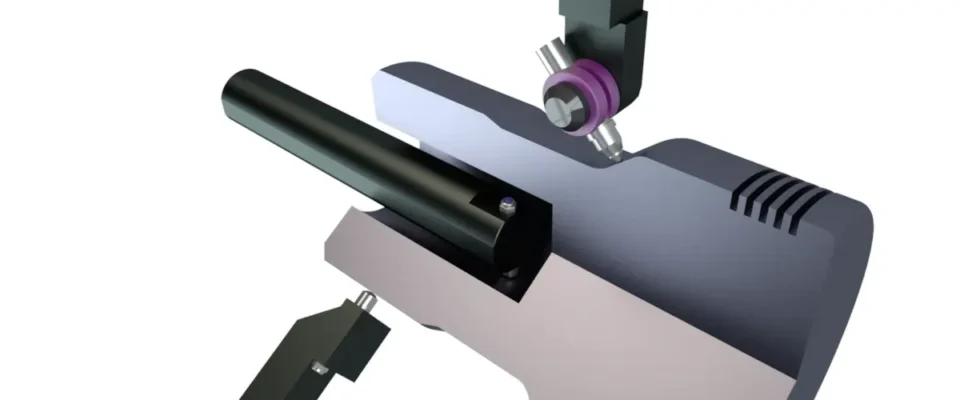
今日、焼入れ鋼は、ピニオン、カムシャフト、クランクシャフト、クラウンホイールの製造など、自動車分野で幅広く使用されている。これらの部品は通常、動的な負荷環境下で使用されるため、疲労強度は高レベルでなければなりません。
このような部品の硬度が45HRCを超えると、ハードマシニングと表現される。
精密ハードターニングは、高硬度部品の加工において従来の研削に取って代わる能力を持つため、産業分野での利用は飛躍的に拡大した。
しかしその後、ハードターニングでは十分な表面仕上げが得られなかったり、表面下層に適切な硬さが得られなかったり、引張残留応力が生じたりして、疲労寿命に好ましくない影響を及ぼすことが判明した。
したがって、ハードターニングのこれらの限界を克服するためには、適切な表面の完全性を得るために、ハードターニングの後にスライドダイヤモンドバニシングのような仕上げ加工が必要となる。
ダイヤモンド・バニシングは、運動学的には旋盤加工に似ているが、切り屑を除去しない仕上げ加工で、球状に研磨され、研磨されたダイヤモンドを持つ変形工具が、加圧された状態で被加工物の表面を滑り、塑性変形を引き起こす。
このプロセスの主なメリットは、耐食性と耐摩耗性の向上、微小硬度の向上、表面粗さの低減、圧縮残留応力の誘発、表面組織の微細化である。
その結果、ワークピースの疲労強度が向上する。このような利点から、硬質旋削鋼部品の研削加工をダイヤモンドバニシングで代用することが可能です。
バニシング加工には、従来型旋盤とCNC旋盤の両方が主に使用される。ワークが回転すると、バニシングヘッドがワークに押し付けられ、軸方向に移動します。ダイヤモンド・バニシング加工の基本的な制御パラメーターは、以下の通りです。
バニシング力(、N)、
バニシング送り (, mm/rev)、
部品の回転速度(rpm)、
またはバニシング速度(m/min)、
とダイヤモンド半径の摩耗(mm)。
これまでのところ、表面粗さ、表面残留応力、微小硬度、微細構造のようなダイヤモンド・バニシングプロセスの出力に対するバニシングパラメータとその相互作用の影響を調査するために、多くの研究が行われてきた。
これらの研究結果は、ダイヤモンドバニシングプロセスの有効性が、適用されるバニシングパラメータの範囲とそれらの相互作用、バニシングされる材料の種類とその硬度、潤滑やダイヤモンド半径の摩耗のようなバニシングプロセスの環境に大きく依存することを示している。
ダイヤモンドのバニシング加工が表面粗さに及ぼす影響を調べるために、以下のリンクをご覧ください。(近日公開予定)